GreenWaste Renewable Energy Digestion Facility
Producing renewable energy from organic waste.
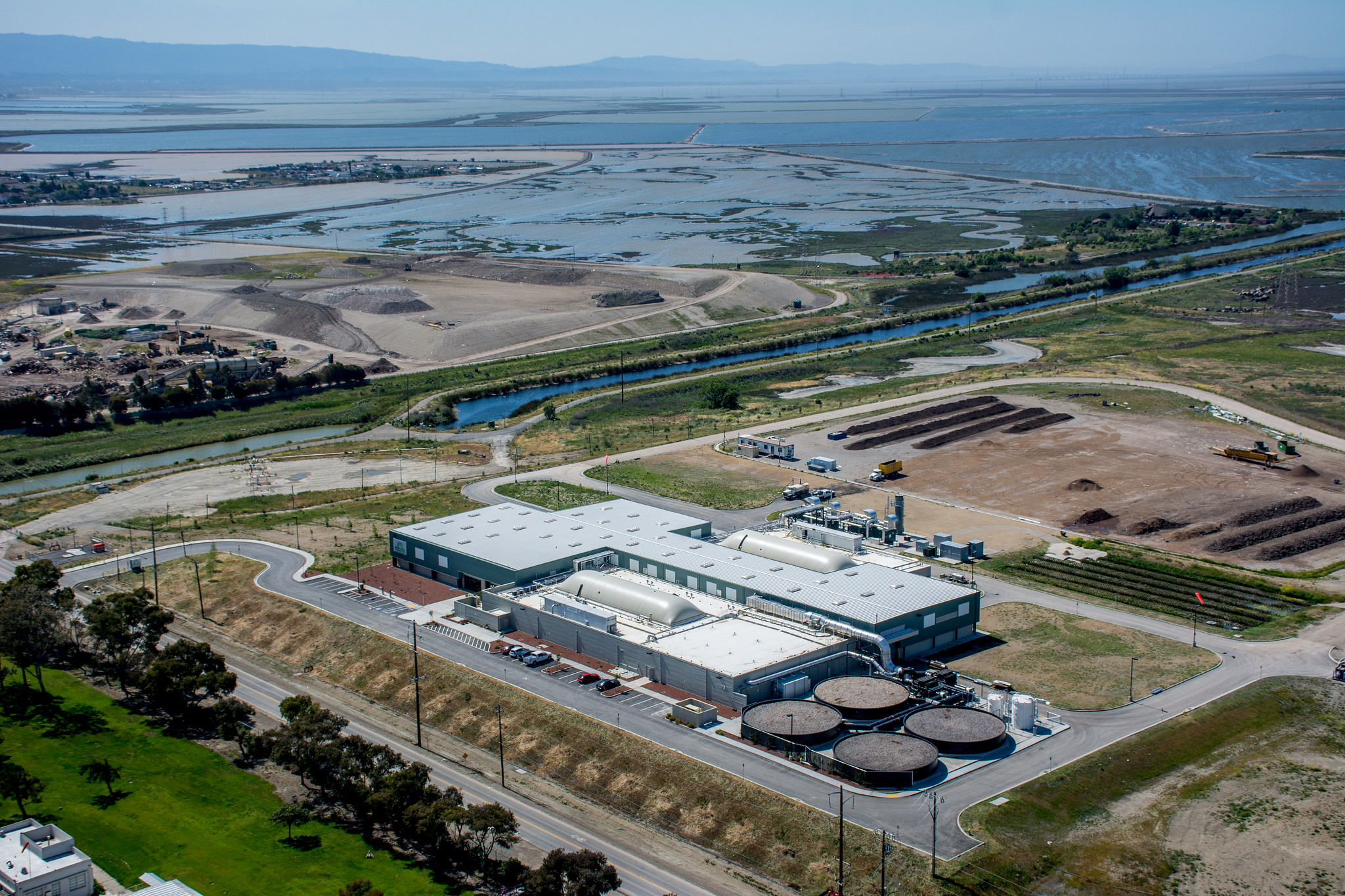
Visit Us Today
What We Process
The GreenWaste Renewable Energy Digestion Facility processes the City of San Jose’s commercial organic waste through a 15-year exclusive organics processing agreement. The organic material includes pre- and post-consumer source separated food waste, residuals from processing wet and dry materials, and yard waste.
The GreenWaste Renewable Energy Digestion Facility processes source-separated residential food waste and yard trimmings and commercial food waste from the City of Palo Alto.
About Us
Anaerobic Digestion Process
Anaerobic Digestion Technology
Permits
Hours and Contact
Opened in 2011, the GreenWaste Renewable Energy Digestion Facility is the largest dry fermentation anaerobic digestion facility in the United States, composting organic material and extracting energy from it during the process. This facility is Green Business Certified and was designed and constructed to align with the most stringent standards for sustainable buildings. It is a fully-enclosed and ventilated organic waste processing and renewable power generation facility, capable of processing up to 90,000 tons per year of organic waste (250 tons-per-day) and generating roughly 1.6MW of clean green renewable power. The facility consists of 16 anaerobic digestion tunnels, 4 in-vessel composting tunnels, and 2 x 800 kW combined heat and power supply units that support electricity production.
Products
Each of the three phases produces:
- Renewable energy (gross generation of 1,600 kW or 13,363,497 kWh-per-year)
- Feedstock for compost (30,000 tons per year)
Energy Use
The facility generates and runs on the 100% renewable energy it produces, providing surplus power to PG&E for distribution to the grid.
Process
Supply Air (Aeration)
- After the organic waste is loaded into the digester, the hatch is closed with a gas seal to maintain process conditions and so that biogas cannot escape.
- In-floor aeration system within each digester creates aerobic digestion conditions to self-heat the material providing significant energy savings.
- Aerobic digestion generally lasts no more than 12 hours.
Percolate Cycle
- Following the initial aeration of the organic material, the aerobic bacteria consume remaining oxygen in the digester to establish anaerobic conditions.
- Organic waste is finely sprayed with conditioned, processed water containing thermophilic microorganisms (percolate) that decompose the waste and produce biogas.
- The percolate is pumped in a closed loop between the digesters.
- Heated and insulated percolate tanks are located beneath the dry digester areas.
Percolate
- Percolate is sprinkled on the material for approximately 20 days causing the production of biogas.
- Percolate is collected in a drainage system, screened for solids, and then overflows back to the percolate tank where it is recharged with thermophilic organisms.
- High quantities of organic acids (arise during the beginning of the process) are stored and degraded to ensure proper pH balance.
- Percolate tanks are of major importance for biogas production.
- Accurate process control of percolate tanks maintains the required thermophilic process temperature.
- The percolate tank is heated by a commercial natural gas heating system or biogas combined heat and power system (CHP) and insulated.
Biogas System
- Production of biogas begins quickly after percolation.
- An embedded system collects the biogas and is stored in roof-mounted double membrane bladders.
- Stored biogas is used to generate electricity in the CHP system.
Exhaust Air
- Before digester doors are opened, percolate dosing is ceased on the 21st day which immediately reduces biogas production.
- Aid is circulated through the same floor aeration system and collected in an exhaust piping system that combusts low-quality biogas in an Environmental Control Device (ECD), and then processes the digester air in a bio-filter.
- The shutdown process is a 4 to 5-hour procedure.
Technology
The GreenWaste Renewable Energy Digestion Facility uses Eggersmann Anlagenbau’s patented Kompoferm high solids dry anaerobic digestion and IVC Plus in-vessel composting technologies, exclusively licensed to and provided by Zero Waste Energy, LLC.
Anaerobic digestion (AD) is a bacterial fermentation process that operates without free oxygen and results in a biogas containing mostly methane and carbon dioxide. AD is also the principal decomposition process occurring in landfills. Biodegradation of organic material occurs in nature principally through the action of aerobic microorganisms. Ultimately, complete oxidation of the carbonaceous organic materials results in the production of carbon dioxide (CO2) and water (H2O). Anaerobic microorganisms degrade the organic matter in the absence of oxygen with ultimate products being CO2 and methane (CH4) collectively called “biogas.” Anaerobic microorganisms occur naturally in low-oxygen environments such as marshes, wetlands, and in the digestive tract of ruminant animals.
There are two basic types of AD technologies, ‘wet’ (low-solids) and ‘dry’ (high-solids). ‘Dry’ digestion is typically defined as having more than 15% of total solids (TS) inside the digester. The wet AD system commonly applies a continuous process flow, where dry AD systems apply either a continuous or batch process.
Although North America has a long history of treating municipal wastewater solids (and more recently agricultural waste such as manure) with a low TS content via wet AD for stabilization and biogas production, only very few commercial-scale AD installations exist to-date that process source-separated organics (SSO) or the organic fraction of municipal solid waste (OFMSW).
In Europe, AD technologies to process SSO and OFMSW on a commercial/industrial scale were developed more than 20 years ago. By the end of 2010, more than 200 AD plants treating SSO and OFMSW with a total installed capacity of about 6 million tons had been built. The trend is towards dry AD technology.
The dry batch digestion technology utilized by the facility requires minimal feedstock processing and no water addition prior to fermentation, significantly reducing pre-processing costs. Rather than wet systems, which move organic waste through a complex system of pullers, mixers, augers, and pumps, the organic material in a dry batch AD system remains stationary in an air-tight tunnel with micro-organisms introduced through a wet sprinkler system in the percolate. No pumps or motors in a dry AD system come into contact with the waste, significantly reducing process requirements while minimizing maintenance downtime. While some wet systems may be capable of generating slightly more biogas on the margin than similarly-sized dry AD systems, the significantly lower internal energy usage and capital and operating costs associated with dry batch systems outweigh the potential biogas generation benefit.
The facility’s dry anaerobic digestion system contains unique features that make it the most cost-effective and productive AD system of any type available for a potential organics processing project:
- Moisture addition and removal not required. Dry solids can be in excess of 50% of the organic waste input.
- The 21-day batch average cycle time compares favorably (up to 25% more productive) than other dry systems.
- Digesters are biologically self-heated through the air system and re-circulation of the liquid percolate through the material, effectively minimizing energy usage.
- The liquid percolate contains the necessary biological constituents and proper pH balance to negate the use of previously digested material (recirculation) needed to start subsequent batches.
- Thermophilic mode of operation improves biogas production and downstream renewable energy applications.
- Odor is controlled through the injection of oxygen into the digester at the end of the process, which helps to strip odors (primarily hydrogen sulfide) and yield a superior product. Exhaust air produced from the shutdown process is oxidized in a bio filter for further odor mitigation.
- In the thermophilic mode of operation, the digestate emerging at the end of the process is free of pathogens (e.g., salmonella) meaning it is a compost product per the US EPA’s Process to Further Reduce Pathogen’s (PFRP) sanitation requirements.
Permits
Hours
Mon. — Fri.: 9 AM- 5 PM
Closed Sat. and Sun.
Address
GreenWaste Renewable Energy Digestion Facility
685 Los Esteros Road
San Jose, CA 95134